The Challenge
The objective of this case study was to lightweight a bracket made out of Aluminium 6061, at the same time ensuring that the bracket maintains its original topology and structural integrity, even as new materials savings are achieved through this innovative lightweighting method.
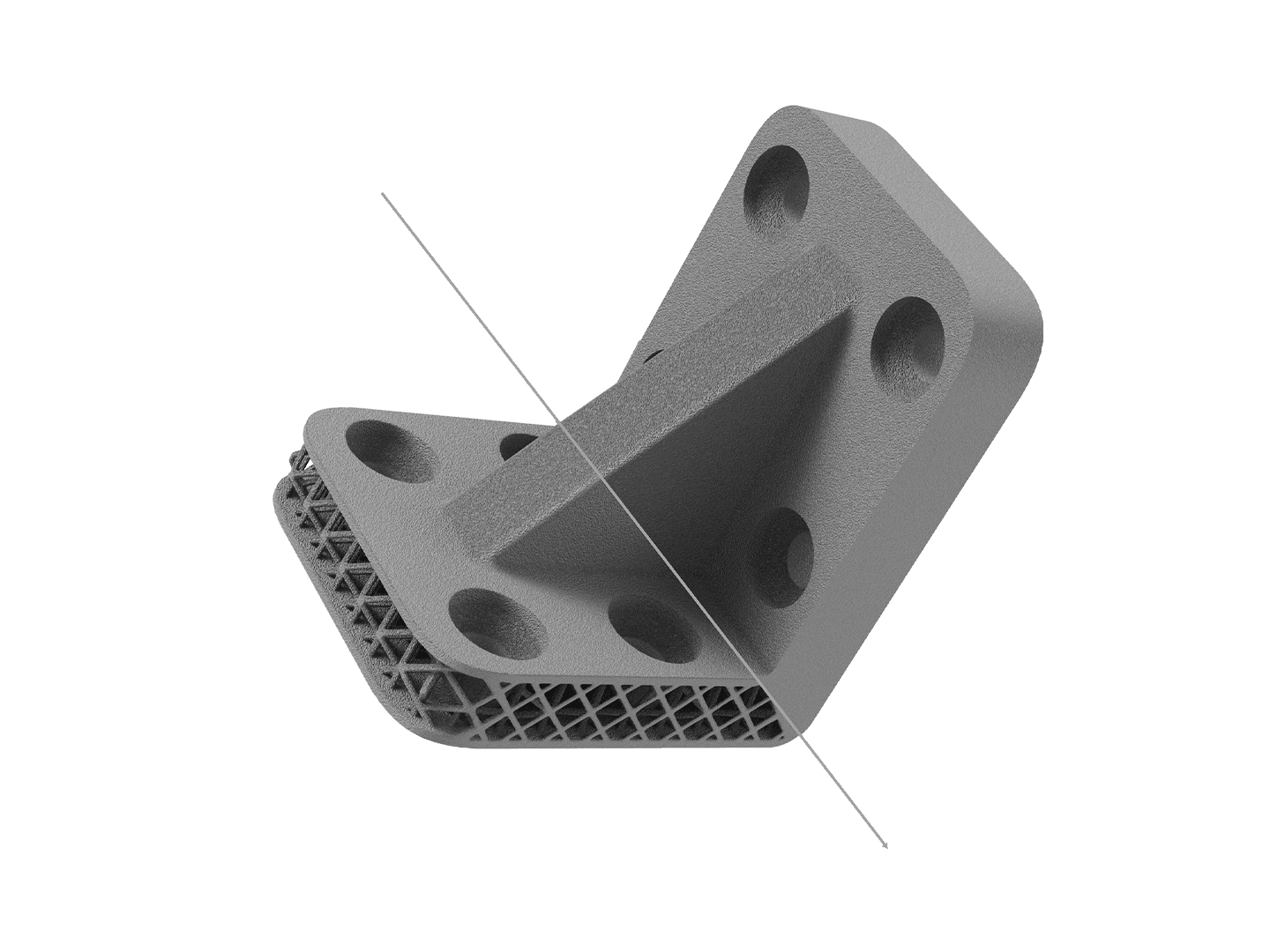